Research Projects
Live Life Time Product and Healing Prediction - Smart Stent
Cardiovascular disease continues to be a major healthcare challenge, claiming millions of lives annually, and driving the need for innovative medical solutions. Traditional non-degradable metal stents are being outpaced by the development of polymer-based and biodegradable metal stents, which offer biocompatibility and effective drug delivery. This work aims to create a computational framework to optimize biodegradable stent design, considering mechanical, chemical corrosion, and drug release effects through a Multiphysics Computational Model. A key goal is to develop a Smart Stent enhanced with deep learning and electronics, capable of real-time evaluation of stent lifespan using data from blood sensors. This innovation promises personalized patient care and improved treatment outcomes, while also driving profitability to sustain further research.
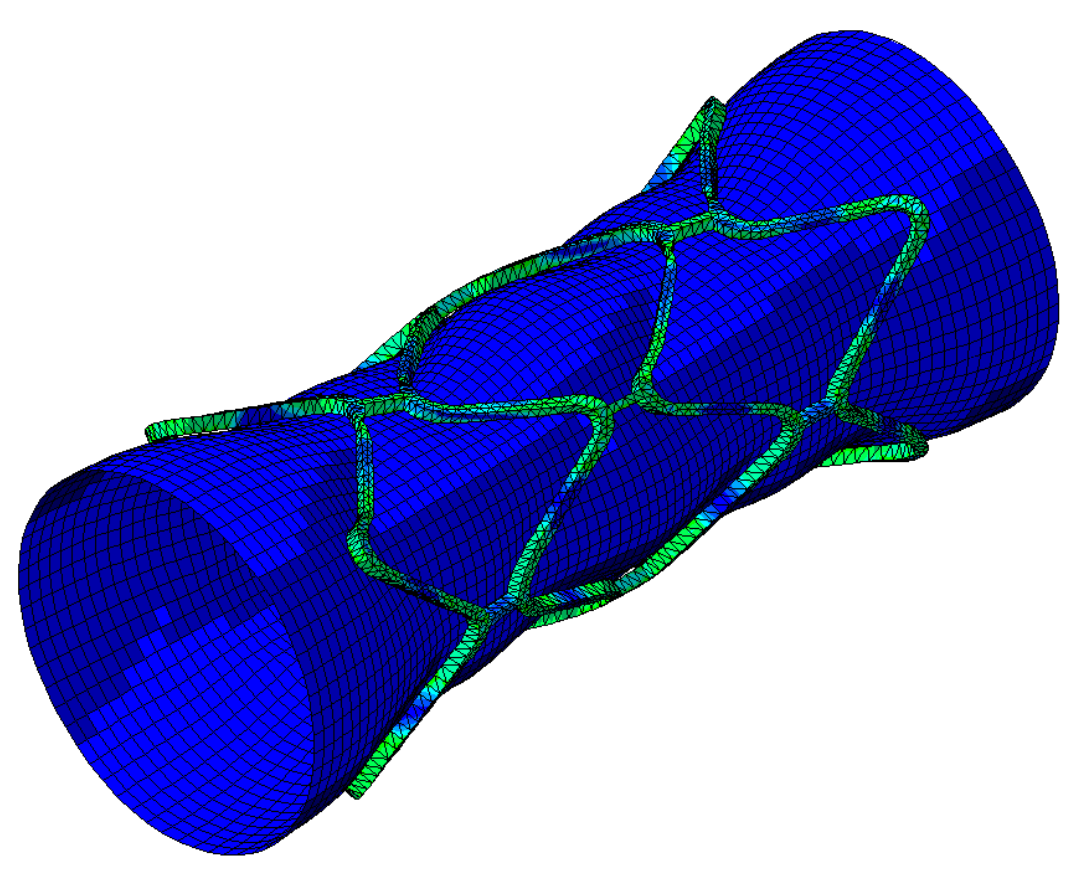
A Computational Model for Atherosclerosis
This project focuses on creating a computational model that integrates mechanics and biology to elucidate atherosclerosis and plaque formation, inspired by recent advancements. The model uniquely incorporates the role of vasa vasorum vessels and considers the artery as a three-layered structure (intima, media, adventitia) with individual material parameters. It also includes pre-stretch formulation to represent biological homeostasis and examines cell behaviors within the arterial wall. The thesis outlines continuum mechanics fundamentals, finite strain theory, and diffusion theory to underpin the new model, comparing its results with existing literature.
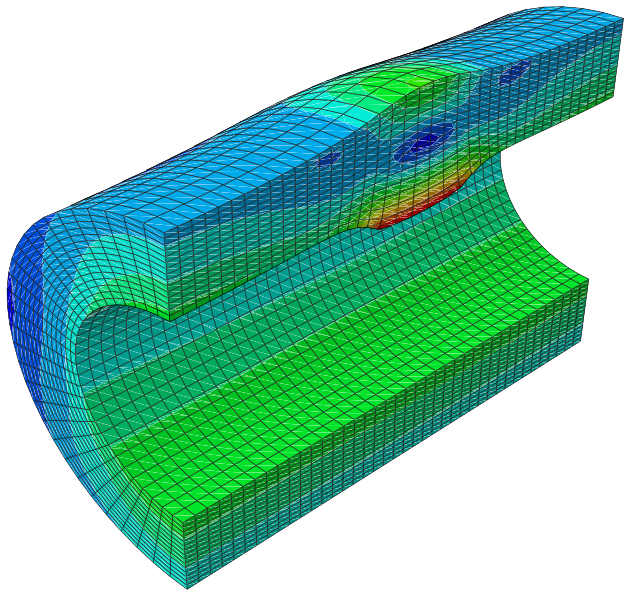
An Enhanced U-Net Deep Learning Approach for Vascular Wall Fracture Analysis
This work presents an efficient deep learning approach for analyzing vascular wall fractures using experimental data, with openly accessible source codes provided for reproduction. Vascular disease, a leading cause of global mortality, requires detailed study of tissue damage for better understanding and treatment. The symmetry-constrained Compact Tension (symconCT) test combined with Digital Image Correlation (DIC) was used to investigate tissue fractures in various aorta specimens. Traditional analysis of biological tissue fractures involves high computational and experimental costs, but deep learning, specifically using the Attention Residual U-Net architecture, offers a promising solution. By training the model on sufficient data, the approach enhances predictive accuracy and reduces the computational and experimental burden.
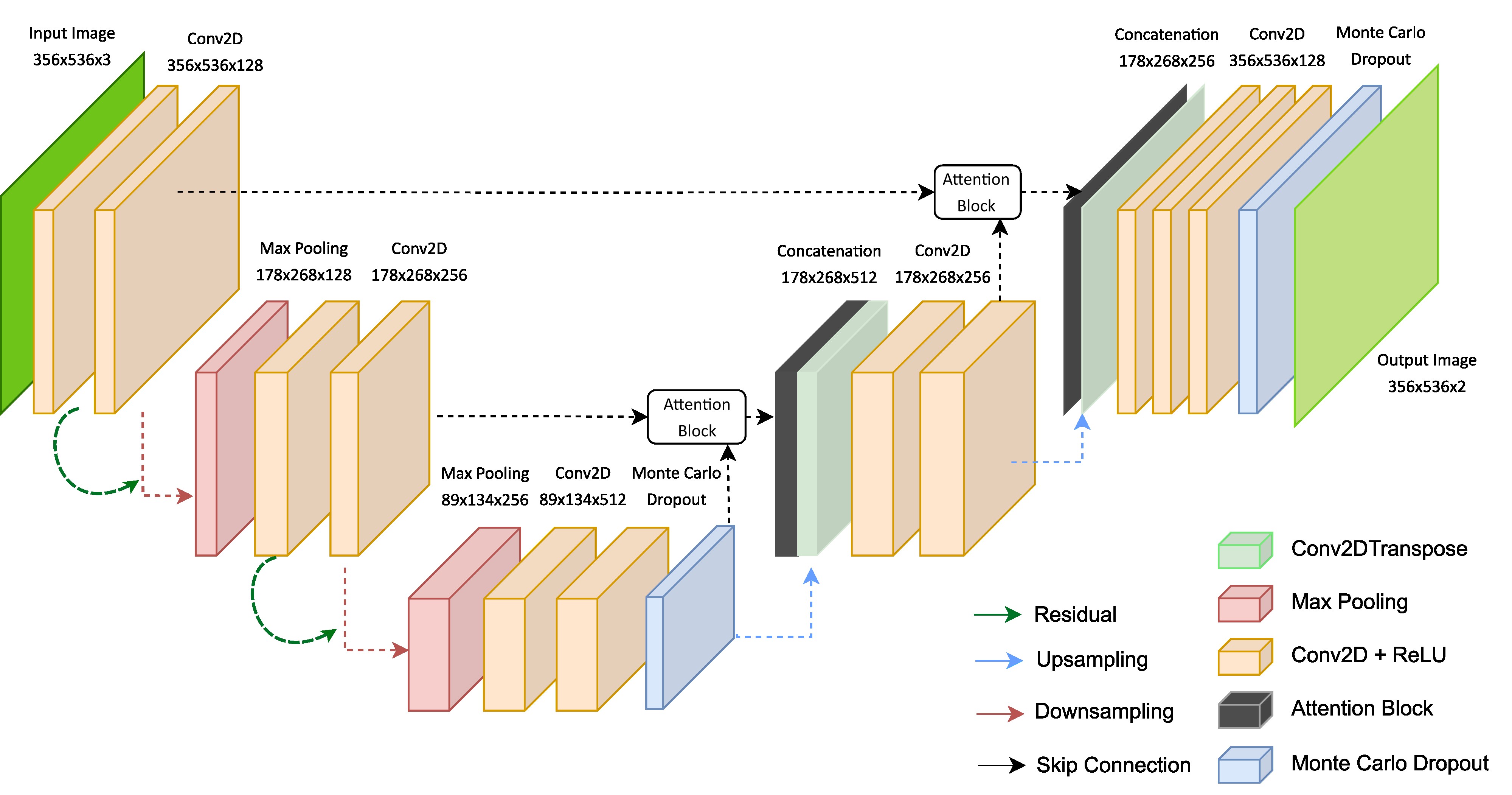
Construction Project - KPIV
This construction project regards the gear mechanism of a milling machine, which it is designed for horizontal machining (peripheral milling) of workpieces, featuring an input shaft and a parallel output shaft in the same plane. It includes a vertical head for optional vertical machining (face milling) and offers four gears for various speeds, switchable via two clutches. Feed movements in all three spatial directions are manually operated via feed screws. The power flow can be redirected vertically using a bevel gear stage without altering speed. The machine aims to machine components with four different feed and cutting speeds but with identical geometries, starting with peripheral milling followed by face milling.
Investigation of dynamic substructuring methods for systems with arbitrary viscous damping under stochastic excitation
During the development of a product, ensuring the quality of mechanical components is essential. One effective method is applying the finite element method to computer-aided design models. However, balancing computational efficiency with accuracy poses a challenge. This project focuses on implementing substructuring methods in mechanical systems with arbitrary viscous damping under stochastic excitation in state space. The Craig-Bampton, Hasselman & Kaplan Adaptation, Beliveau & Soucy, and de Kraker’s reduction methods are evaluated for their ability to approximate eigenvalues and minimize standard deviation errors compared to exact solutions. The project covers fundamental vibration theory, modal analysis, and stochastic field concepts. Simulations investigate the impact of modes, damping, and geometry on computational efficiency and accuracy, providing insights for future research directions.
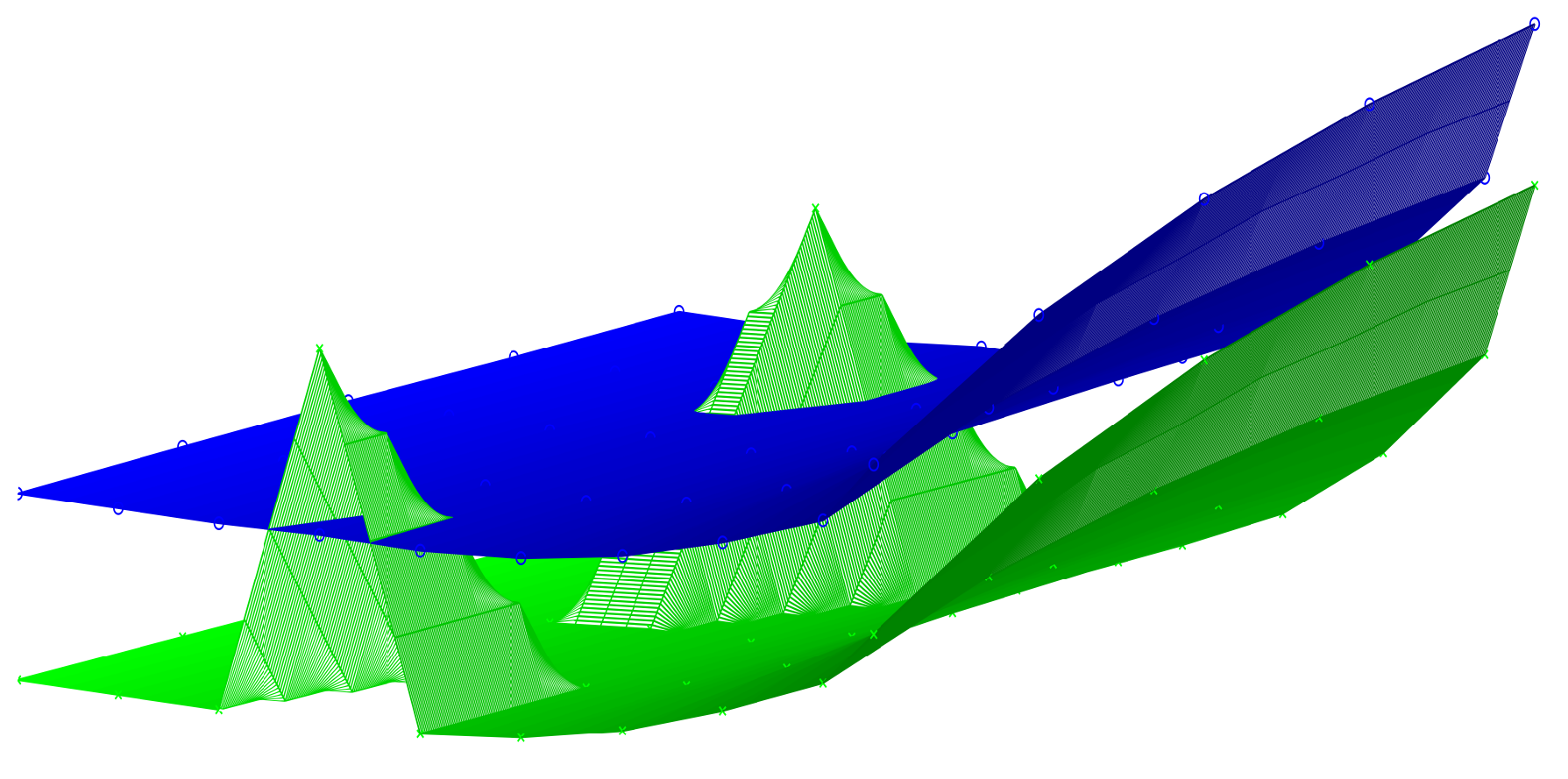
Development of a mesh generator and implementation of the discontinuous Galerkin Finite Element Method in 3D to avoid geometric stiffening effects.
The effect of shear locking manifests as the inability of finite elements using classical Lagrange polynomial approaches of lower order to accurately depict deformation in bending-dominant problems. Consequently, the convergence rate of displacement solutions decreases compared to elements using higher-order approaches such as quadratic polynomials for displacement degrees of freedom. The use of the discontinuous Galerkin Finite Element Method (dG-FEM) provides a formulation capable of circumventing this phenomenon. By introducing discontinuities in the displacement field between adjacent elements, the method mitigates stiffness in bending, resulting in smoother behavior. Within the scope of this project, a mesh generator is to be developed as the foundation for automated creation of three-dimensional discontinuous meshes. Implementation will occur in Matlab, where continuous meshes from FEAP will be imported and manipulated to generate a new input file directly usable with the 3D dG element. Furthermore, the existing 2D dG element for linear elasticity will be extended to 3D. Through suitable numerical examples, the project aims to demonstrate convergence behavior in bending-dominant problems and address the issue of shear locking.
Construction Project - KPIII
This project involved the designing of a machine. It's about creating a gearbox for a lathe, a machine used for shaping metal parts. The gearbox controls two key movements: the rotation of the chuck holding the workpiece and the back-and-forth travel of the cutting tool. It was developed to have different speeds for the tool slide and an overload clutch to ensure safety during operation. The design considered technical specifications, customer needs, and a sketch of the parts the lathe will produce.